Galvanic cells designed specifically to function as electrical power supplies are called batteries. A variety of both single-use batteries (primary cells) and rechargeable batteries (secondary cells) are commercially available to serve a variety of applications, with important specifications including voltage, size, and lifetime. Fuel cells, sometimes called flow batteries, are devices that harness the energy of spontaneous redox reactions normally associated with combustion processes. Like batteries, fuel cells enable the reaction’s electron transfer via an external circuit, but they require continuous input of the redox reactants (fuel and oxidant) from an external reservoir. Fuel cells are typically much more efficient in converting the energy released by the reaction to useful work in comparison to internal combustion engines. Spontaneous oxidation of metals by natural electrochemical processes is called corrosion, familiar examples including the rusting of iron and the tarnishing of silver. Corrosion process involve the creation of a galvanic cell in which different sites on the metal object function as anode and cathode, with the corrosion taking place at the anodic site. Approaches to preventing corrosion of metals include use of a protective coating of zinc (galvanization) and the use of sacrificial anodes connected to the metal object (cathodic protection). Nonspontaneous redox processes may be forced to occur in electrochemical cells by the application of an appropriate potential using an external power source—a process known as electrolysis. Electrolysis is the basis for certain ore refining processes, the industrial production of many chemical commodities, and the electroplating of metal coatings on various products. Measurement of the current flow during electrolysis permits stoichiometric calculations.
38.1 Batteries and Fuel Cells
Learning Objectives
By the end of this section, you will be able to:
- Describe the electrochemistry associated with several common batteries
- Distinguish the operation of a fuel cell from that of a battery
There are many technological products associated with the past two centuries of electrochemistry research, none more immediately obvious than the battery. A battery is a galvanic cell that has been specially designed and constructed in a way that best suits its intended use a source of electrical power for specific applications. Among the first successful batteries was the Daniell cell, which relied on the spontaneous oxidation of zinc by copper(II) ions (Figure 38.1):
Figure 38.1
Illustration of a Daniell cell taken from a 1904 journal publication (left) along with a simplified illustration depicting the electrochemistry of the cell (right). The 1904 design used a porous clay pot to both contain one of the half-cell’s content and to serve as a salt bridge to the other half-cell.
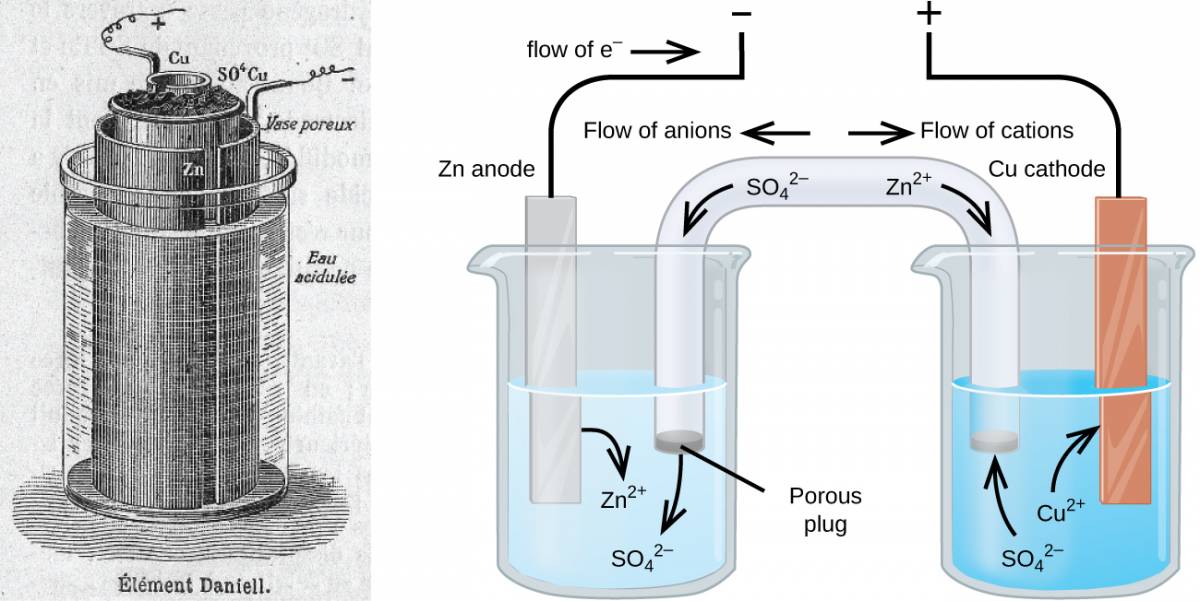
Modern batteries exist in a multitude of forms to accommodate various applications, from tiny button batteries that provide the modest power needs of a wristwatch to the very large batteries used to supply backup energy to municipal power grids. Some batteries are designed for single-use applications and cannot be recharged (primary cells), while others are based on conveniently reversible cell reactions that allow recharging by an external power source (secondary cells). This section will provide a summary of the basic electrochemical aspects of several batteries familiar to most consumers, and will introduce a related electrochemical device called a fuel cell that can offer improved performance in certain applications.
Visit this site to learn more about batteries.
38.2 Single-Use Batteries
A common primary battery is the dry cell, which uses a zinc can as both container and anode (“–” terminal) and a graphite rod as the cathode (“+” terminal). The Zn can is filled with an electrolyte paste containing manganese(IV) oxide, zinc(II) chloride, ammonium chloride, and water. A graphite rod is immersed in the electrolyte paste to complete the cell. The spontaneous cell reaction involves the oxidation of zinc:
and the reduction of manganese(IV)
which together yield the cell reaction:
The voltage (cell potential) of a dry cell is approximately 1.5 V. Dry cells are available in various sizes (e.g., D, C, AA, AAA). All sizes of dry cells comprise the same components, and so they exhibit the same voltage, but larger cells contain greater amounts of the redox reactants and therefore are capable of transferring correspondingly greater amounts of charge. Like other galvanic cells, dry cells may be connected in series to yield batteries with greater voltage outputs, if needed.
Figure 38.2
A schematic diagram shows a typical dry cell.
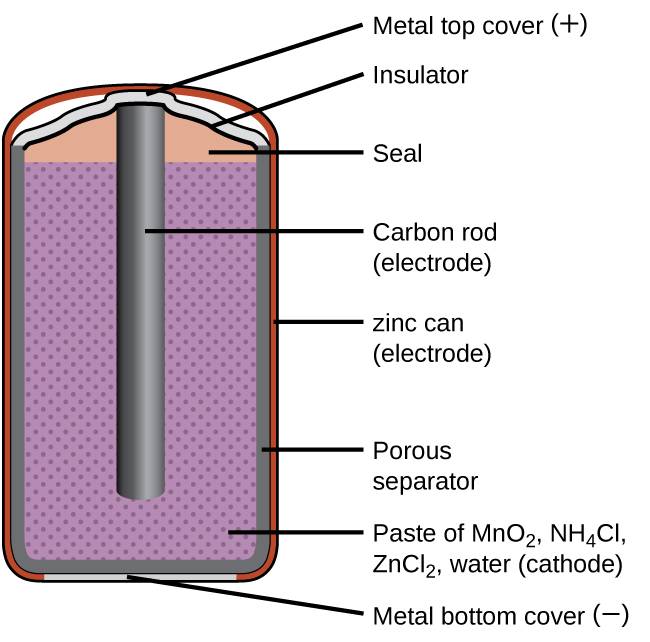
Visit this site to learn more about zinc-carbon batteries.
Alkaline batteries (Figure 38.3) were developed in the 1950s to improve on the performance of the dry cell, and they were designed around the same redox couples. As their name suggests, these types of batteries use alkaline electrolytes, often potassium hydroxide. The reactions are
An alkaline battery can deliver about three to five times the energy of a zinc-carbon dry cell of similar size. Alkaline batteries are prone to leaking potassium hydroxide, so they should be removed from devices for long-term storage. While some alkaline batteries are rechargeable, most are not. Attempts to recharge an alkaline battery that is not rechargeable often leads to rupture of the battery and leakage of the potassium hydroxide electrolyte.
Figure 38.3
Alkaline batteries were designed as improved replacements for zinc-carbon (dry cell) batteries.
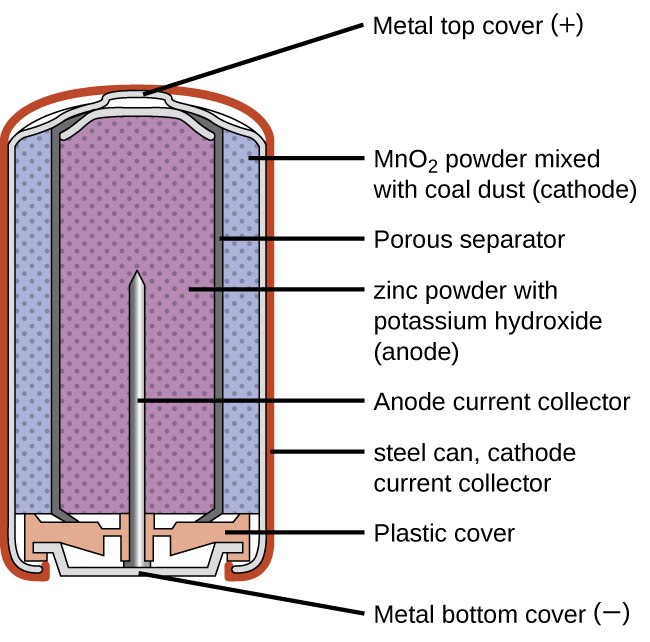
Visit this site to learn more about alkaline batteries.
38.3 Rechargeable (Secondary) Batteries
Nickel-cadmium, or NiCd, batteries (Figure 38.4) consist of a nickel-plated cathode, cadmium-plated anode, and a potassium hydroxide electrode. The positive and negative plates, which are prevented from shorting by the separator, are rolled together and put into the case. This is a “jelly-roll” design and allows the NiCd cell to deliver much more current than a similar-sized alkaline battery. The reactions are
When properly treated, a NiCd battery can be recharged about 1000 times. Cadmium is a toxic heavy metal so NiCd batteries should never be ruptured or incinerated, and they should be disposed of in accordance with relevant toxic waste guidelines.
Figure 38.4
NiCd batteries use a “jelly-roll” design that significantly increases the amount of current the battery can deliver as compared to a similar-sized alkaline battery.
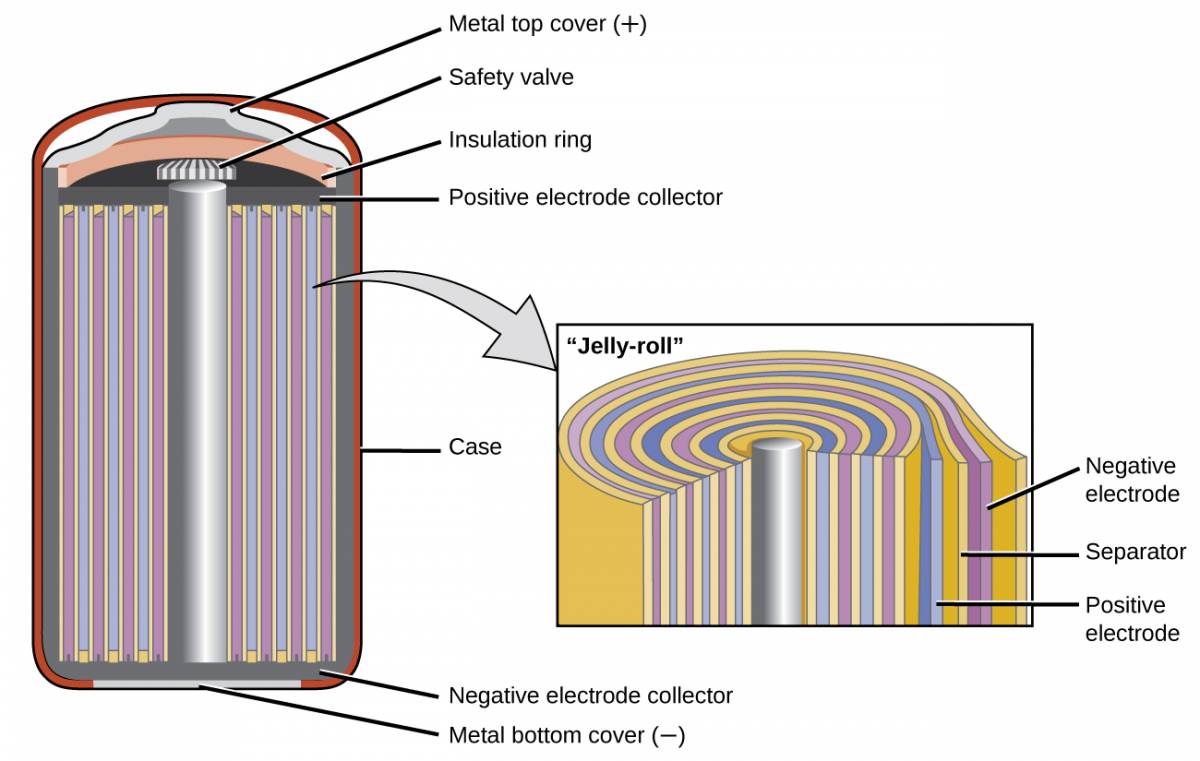
Visit this site for more information about nickel cadmium rechargeable batteries.
Lithium ion batteries (Figure 38.5) are among the most popular rechargeable batteries and are used in many portable electronic devices. The reactions are
The variable stoichiometry of the cell reaction leads to variation in cell voltages, but for typical conditions, x is usually no more than 0.5 and the cell voltage is approximately 3.7 V. Lithium batteries are popular because they can provide a large amount current, are lighter than comparable batteries of other types, produce a nearly constant voltage as they discharge, and only slowly lose their charge when stored.
Figure 38.5
In a lithium ion battery, charge flows as the lithium ions are transferred between the anode and cathode.
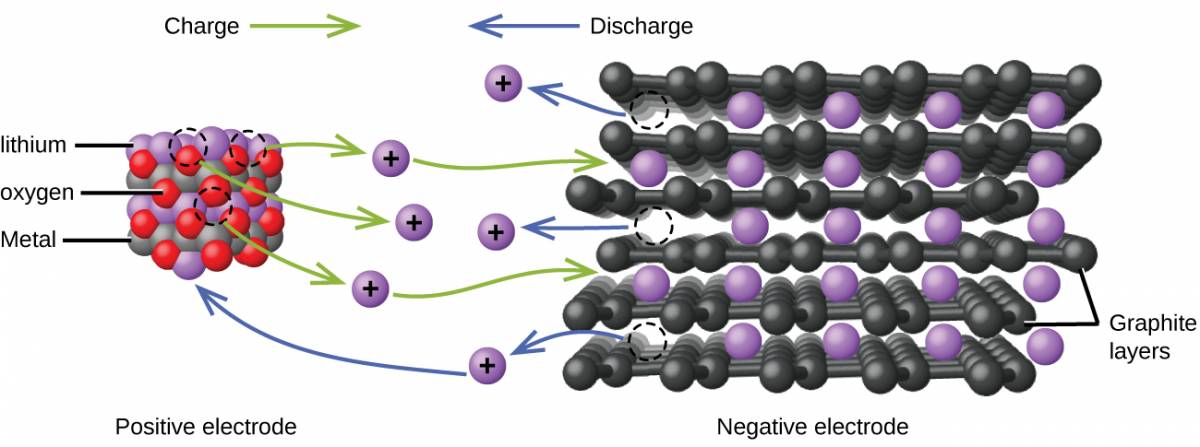
Visit this site for more information about lithium ion batteries.
The lead acid battery (Figure 38.6) is the type of secondary battery commonly used in automobiles. It is inexpensive and capable of producing the high current required by automobile starter motors. The reactions for a lead acid battery are
Each cell produces 2 V, so six cells are connected in series to produce a 12-V car battery. Lead acid batteries are heavy and contain a caustic liquid electrolyte, H2SO4(aq), but are often still the battery of choice because of their high current density. Since these batteries contain a significant amount of lead, they must always be disposed of properly.
Figure 38.6
The lead acid battery in your automobile consists of six cells connected in series to give 12 V.
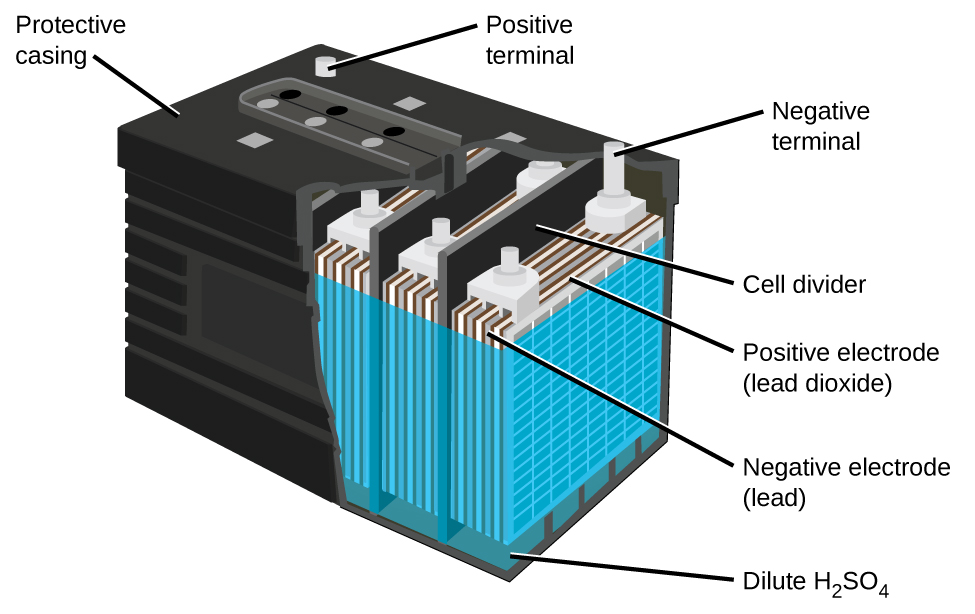
Visit this site for more information about lead acid batteries.
38.4 Fuel Cells
A fuel cell is a galvanic cell that uses traditional combustive fuels, most often hydrogen or methane, that are continuously fed into the cell along with an oxidant. (An alternative, but not very popular, name for a fuel cell is a flow battery.) Within the cell, fuel and oxidant undergo the same redox chemistry as when they are combusted, but via a catalyzed electrochemical that is significantly more efficient. For example, a typical hydrogen fuel cell uses graphite electrodes embedded with platinum-based catalysts to accelerate the two half-cell reactions:
Figure 38.7
In this hydrogen fuel cell, oxygen from the air reacts with hydrogen, producing water and electricity.
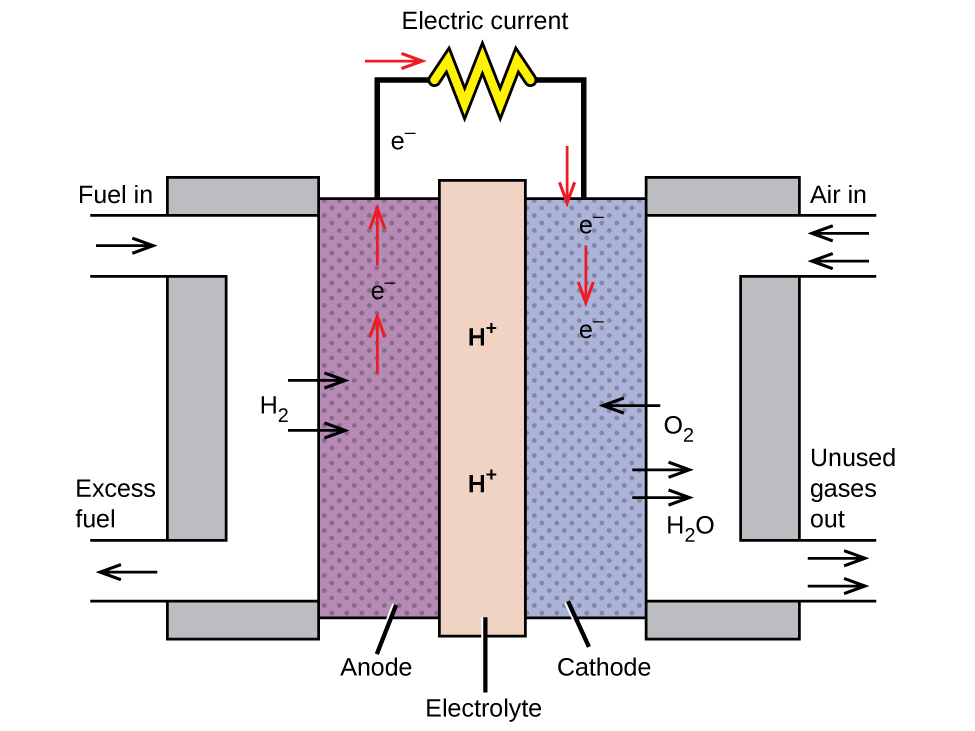
These types of fuel cells generally produce voltages of approximately 1.2 V. Compared to an internal combustion engine, the energy efficiency of a fuel cell using the same redox reaction is typically more than double (~20%–25% for an engine versus ~50%–75% for a fuel cell). Hydrogen fuel cells are commonly used on extended space missions, and prototypes for personal vehicles have been developed, though the technology remains relatively immature.
Check out this link to learn more about fuel cells.
38.5 Corrosion
Learning Objectives
By the end of this section, you will be able to:
- Define corrosion
- List some of the methods used to prevent or slow corrosion
Corrosion is usually defined as the degradation of metals by a naturally occurring electrochemical process. The formation of rust on iron, tarnish on silver, and the blue-green patina that develops on copper are all examples of corrosion. The total cost of corrosion remediation in the United States is significant, with estimates in excess of half a trillion dollars a year.
38.5.1 CHEMISTRY IN EVERYDAY LIFE
Statue of Liberty: Changing Colors
The Statue of Liberty is a landmark every American recognizes. The Statue of Liberty is easily identified by its height, stance, and unique blue-green color (Figure 38.8). When this statue was first delivered from France, its appearance was not green. It was brown, the color of its copper “skin.” So how did the Statue of Liberty change colors? The change in appearance was a direct result of corrosion. The copper that is the primary component of the statue slowly underwent oxidation from the air. The oxidation-reduction reactions of copper metal in the environment occur in several steps. Copper metal is oxidized to copper(I) oxide (Cu2O), which is red, and then to copper(II) oxide, which is black
Coal, which was often high in sulfur, was burned extensively in the early part of the last century. As a result, atmospheric sulfur trioxide, carbon dioxide, and water all reacted with the CuO
These three compounds are responsible for the characteristic blue-green patina seen on the Statue of Liberty (and other outdoor copper structures). Fortunately, formation of patina creates a protective layer on the copper surface, preventing further corrosion of the underlying copper. The formation of the protective layer is called passivation, a phenomenon discussed further in another chapter of this text.
Perhaps the most familiar example of corrosion is the formation of rust on iron. Iron will rust when it is exposed to oxygen and water. Rust formation involves the creation of a galvanic cell at an iron surface, as illustrated in Figure 38.8. The relevant redox reactions are described by the following equations:
Further reaction of the iron(II) product in humid air results in the production of an iron(III) oxide hydrate known as rust:
The stoichiometry of the hydrate varies, as indicated by the use of x in the compound formula. Unlike the patina on copper, the formation of rust does not create a protective layer and so corrosion of the iron continues as the rust flakes off and exposes fresh iron to the atmosphere.
Figure 38.9
Corrosion can occur when a painted iron or steel surface is exposed to the environment by a scratch through the paint. A galvanic cell results that may be approximated by the simplified cell schematic Fe(s) | Fe2+(aq) ||O2(aq), H2O(l) | Fe(s).
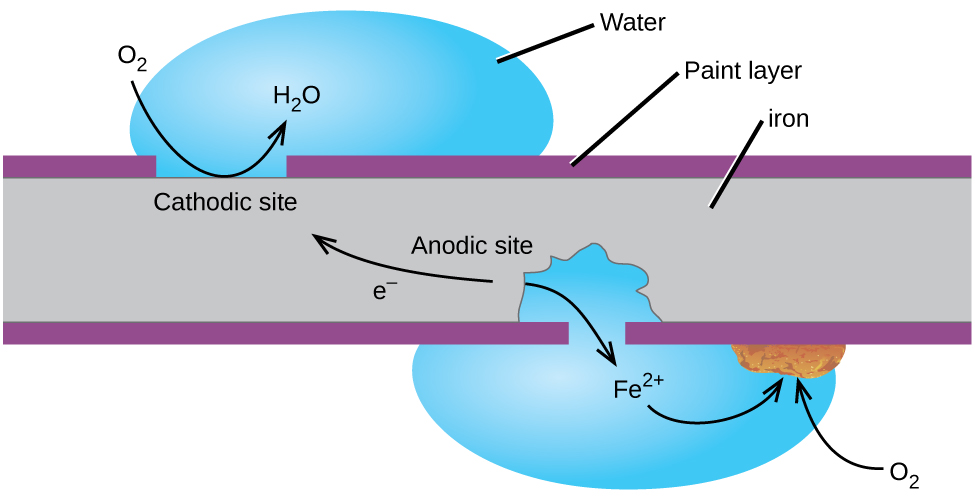
One way to keep iron from corroding is to keep it painted. The layer of paint prevents the water and oxygen necessary for rust formation from coming into contact with the iron. As long as the paint remains intact, the iron is protected from corrosion.
Other strategies include alloying the iron with other metals. For example, stainless steel is an alloy of iron containing a small amount of chromium. The chromium tends to collect near the surface, where it corrodes and forms a passivating an oxide layer that protects the iron.
Iron and other metals may also be protected from corrosion by galvanization, a process in which the metal to be protected is coated with a layer of a more readily oxidized metal, usually zinc. When the zinc layer is intact, it prevents air from contacting the underlying iron and thus prevents corrosion. If the zinc layer is breached by either corrosion or mechanical abrasion, the iron may still be protected from corrosion by a cathodic protection process, which is described in the next paragraph.
Another important way to protect metal is to make it the cathode in a galvanic cell. This is cathodic protection and can be used for metals other than just iron. For example, the rusting of underground iron storage tanks and pipes can be prevented or greatly reduced by connecting them to a more active metal such as zinc or magnesium (Figure 38.10). This is also used to protect the metal parts in water heaters. The more active metals (lower reduction potential) are called sacrificial anodes because as they get used up as they corrode (oxidize) at the anode. The metal being protected serves as the cathode for the reduction of oxygen in air, and so it simply serves to conduct (not react with) the electrons being transferred. When the anodes are properly monitored and periodically replaced, the useful lifetime of the iron storage tank can be greatly extended.
Figure 38.10
Cathodic protection is a useful approach to electrochemically preventing corrosion of underground storage tanks.

38.6 Electrolysis
By the end of this section, you will be able to:
- Describe the process of electrolysis
- Compare the operation of electrolytic cells with that of galvanic cells
- Perform stoichiometric calculations for electrolytic processes
Electrochemical cells in which spontaneous redox reactions take place (galvanic cells) have been the topic of discussion so far in this chapter. In these cells, electrical work is done by a redox system on its surroundings as electrons produced by the redox reaction are transferred through an external circuit. This final section of the chapter will address an alternative scenario in which an external circuit does work on a redox system by imposing a voltage sufficient to drive an otherwise nonspontaneous reaction, a process known as electrolysis. A familiar example of electrolysis is recharging a battery, which involves use of an external power source to drive the spontaneous (discharge) cell reaction in the reverse direction, restoring to some extent the composition of the half-cells and the voltage of the battery. Perhaps less familiar is the use of electrolysis in the refinement of metallic ores, the manufacture of commodity chemicals, and the electroplating of metallic coatings on various products (e.g., jewelry, utensils, auto parts). To illustrate the essential concepts of electrolysis, a few specific processes will be considered.
38.7 The Electrolysis of Molten Sodium Chloride
Metallic sodium, Na, and chlorine gas, Cl2, are used in numerous applications, and their industrial production relies on the large-scale electrolysis of molten sodium chloride, NaCl(l). The industrial process typically uses a Downs cell similar to the simplified illustration shown in Figure 38.11. The reactions associated with this process are:
The cell potential for the above process is negative, indicating the reaction as written (decomposition of liquid NaCl) is not spontaneous. To force this reaction, a positive potential of magnitude greater than the negative cell potential must be applied to the cell.
Figure 38.11
Cells of this sort (a cell for the electrolysis of molten sodium chloride) are used in the Downs process for production of sodium and chlorine, and they typically use iron cathodes and carbon anodes.

38.8 The Electrolysis of Water
Water may be electrolytically decomposed in a cell similar to the one illustrated in Figure 38.12. To improve electrical conductivity without introducing a different redox species, the hydrogen ion concentration of the water is typically increased by addition of a strong acid. The redox processes associated with this cell are
Again, the cell potential as written is negative, indicating a nonspontaneous cell reaction that must be driven by imposing a cell voltage greater than +1.229 V. Keep in mind that standard electrode potentials are used to inform thermodynamic predictions here, though the cell is not operating under standard state conditions. Therefore, at best, calculated cell potentials should be considered ballpark estimates.
Figure 38.12
The electrolysis of water produces stoichiometric amounts of oxygen gas at the anode and hydrogen at the anode.
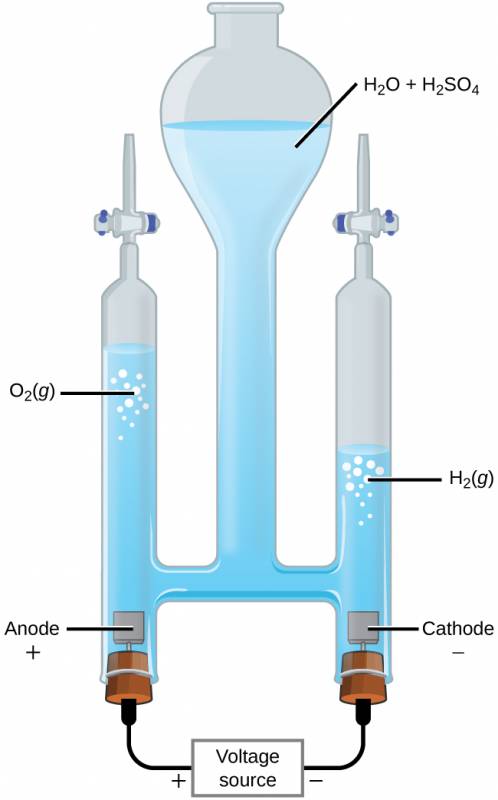
38.9 The Electrolysis of Aqueous Sodium Chloride
When aqueous solutions of ionic compounds are electrolyzed, the anode and cathode half-reactions may involve the electrolysis of either water species (H2O, H+, OH-) or solute species (the cations and anions of the compound). As an example, the electrolysis of aqueous sodium chloride could involve either of these two anode reactions:
The standard electrode (reduction) potentials of these two half-reactions indicate water may be oxidized at a less negative/more positive potential (–1.229 V) than chloride ion (–1.358 V). Thermodynamics thus predicts that water would be more readily oxidized, though in practice it is observed that both water and chloride ion are oxidized under typical conditions, producing a mixture of oxygen and chlorine gas.
Turning attention to the cathode, the possibilities for reduction are:
Comparison of these standard half-reaction potentials suggests the reduction of hydrogen ion is thermodynamically favored. However, in a neutral aqueous sodium chloride solution, the concentration of hydrogen ion is far below the standard state value of 1 M (approximately 10-7 M), and so the observed cathode reaction is actually reduction of water. The net cell reaction in this case is then
This electrolysis reaction is part of the chlor-alkali process used by industry to produce chlorine and sodium hydroxide (lye).
38.9.1 CHEMISTRY IN EVERYDAY LIFE
Electroplating
An important use for electrolytic cells is in electroplating. Electroplating results in a thin coating of one metal on top of a conducting surface. Reasons for electroplating include making the object more corrosion resistant, strengthening the surface, producing a more attractive finish, or for purifying metal. The metals commonly used in electroplating include cadmium, chromium, copper, gold, nickel, silver, and tin. Common consumer products include silver-plated or gold-plated tableware, chrome-plated automobile parts, and jewelry. The silver plating of eating utensils is used here to illustrate the process. (Figure 38.13).
In the figure, the anode consists of a silver electrode, shown on the left. The cathode is located on the right and is the spoon, which is made from inexpensive metal. Both electrodes are immersed in a solution of silver nitrate. Applying a sufficient potential results in the oxidation of the silver anode
and reduction of silver ion at the (spoon) cathode:
The net result is the transfer of silver metal from the anode to the cathode. Several experimental factors must be carefully controlled to obtain high-quality silver coatings, including the exact composition of the electrolyte solution, the cell voltage applied, and the rate of the electrolysis reaction (electrical current).
38.10 Quantitative Aspects of Electrolysis
Electrical current is defined as the rate of flow for any charged species. Most relevant to this discussion is the flow of electrons. Current is measured in a composite unit called an ampere, defined as one coulomb per second (A = 1 C/s). The charge transferred, Q, by passage of a constant current, I, over a specified time interval, t, is then given by the simple mathematical product
When electrons are transferred during a redox process, the stoichiometry of the reaction may be used to derive the total amount of (electronic) charge involved. For example, the generic reduction process
involves the transfer of n mole of electrons. The charge transferred is, therefore,
where F is Faraday’s constant, the charge in coulombs for one mole of electrons. If the reaction takes place in an electrochemical cell, the current flow is conveniently measured, and it may be used to assist in stoichiometric calculations related to the cell reaction.
Converting Current to Moles of Electrons
In one process used for electroplating silver, a current of 10.23 A was passed through an electrolytic cell for exactly 1 hour. How many moles of electrons passed through the cell? What mass of silver was deposited at the cathode from the silver nitrate solution?
Solution
Faraday’s constant can be used to convert the charge (
Q) into moles of electrons (
n). The charge is the current (
I) multiplied by the time
From the problem, the solution contains AgNO3, so the reaction at the cathode involves 1 mole of electrons for each mole of silver
The atomic mass of silver is 107.9 g/mol, so
Check Your Learning
Aluminum metal can be made from aluminum(III) ions by electrolysis. What is the half-reaction at the cathode? What mass of aluminum metal would be recovered if a current of 25.0 A passed through the solution for 15.0 minutes?
0.0777 mol Al = 2.10 g Al.
Time Required for Deposition
In one application, a 0.010-mm layer of chromium must be deposited on a part with a total surface area of 3.3 m
2 from a solution of containing chromium(III) ions. How long would it take to deposit the layer of chromium if the current was 33.46 A? The density of chromium (metal) is 7.19 g/cm
3.
Solution
First, compute the volume of chromium that must be produced (equal to the product of surface area and thickness):
Use the computed volume and the provided density to calculate the molar amount of chromium required:
The stoichiometry of the chromium(III) reduction process requires three moles of electrons for each mole of chromium(0) produced, and so the total charge required is:
Finally, if this charge is passed at a rate of 33.46 C/s, the required time is:
Check Your Learning
What mass of zinc is required to galvanize the top of a 3.00 m
5.50 m sheet of iron to a thickness of 0.100 mm of zinc? If the zinc comes from a solution of Zn(NO
3)
2 and the current is 25.5 A, how long will it take to galvanize the top of the iron? The density of zinc is 7.140 g/cm
3.
11.8 kg Zn requires 382 hours.